In the world of product development, achieving efficiency, quality, and cost-effectiveness is essential for success. DFX Analysis (Design for Excellence) is a critical methodology that has revolutionized product design and manufacturing. It helps optimize products throughout their lifecycle, ensuring they meet performance requirements while keeping costs low. In this article, we will explore DFX analysis, its importance in product design, and how it leads to smarter and more efficient product development.
What is DFX Analysis?
DFX (Design for Excellence) is a holistic approach to product design that focuses on optimizing multiple factors such as manufacturability, cost, quality, reliability, sustainability, and ease of maintenance. Unlike traditional design approaches, DFX incorporates these considerations from the very beginning of the product development process.
The Main Components of DFX include:
- Design for Manufacturing (DFM): Optimizing the product for efficient manufacturing.
- Design for Assembly (DFA): Reducing assembly complexity and improving ease of assembly.
- Design for Reliability (DFR): Ensuring the product performs reliably over time.
- Design for Cost (DFC): Reducing the product’s cost without compromising quality.
- Design for Sustainability (DFS): Incorporating environmental considerations into the design.
By addressing all of these factors during the design phase, DFX analysis helps companies reduce errors, minimize waste, and speed up time to market.
Why DFX Analysis is Crucial for Smarter Product Design
In today’s competitive marketplace, businesses need to streamline their product development processes to stay ahead of the curve. Here’s why DFX analysis is key to creating smarter products:
1. Cost Efficiency
One of the primary goals of DFX analysis is to reduce the overall product cost without sacrificing quality. Traditional product design often involves making changes late in the development process, which can be expensive and time-consuming. DFX allows for early identification of potential cost-saving opportunities, such as reducing the number of components, selecting more affordable materials, and optimizing production methods. By considering these factors early, companies can avoid costly redesigns and unnecessary expenses.
2. Improved Manufacturability
Design for Manufacturing (DFM) is a key aspect of DFX analysis. It ensures that the product is designed in a way that makes it easier and more cost-effective to manufacture. By focusing on simplifying the design and choosing manufacturing-friendly materials, DFM helps companies produce high-quality products with fewer defects and at a lower cost. It also helps minimize production time, enabling businesses to scale up their production processes more efficiently.
3. Faster Time to Market
A well-executed DFX analysis can significantly shorten the time it takes to bring a product to market. By addressing manufacturability, assembly, and reliability during the design phase, companies can avoid delays caused by unforeseen production issues or design flaws. The result is a faster and smoother product development cycle, allowing businesses to meet market demand more quickly and stay ahead of competitors.
4. Higher Product Quality
Design for Reliability (DFR) is another crucial element of DFX analysis. By focusing on the long-term performance and durability of the product, DFR helps ensure that the product meets customer expectations and remains functional over time. Incorporating reliable components, rigorous testing, and quality control measures throughout the design process improves product performance, reduces the likelihood of defects, and enhances customer satisfaction.
5. Sustainability
As environmental concerns continue to grow, Design for Sustainability (DFS) is becoming increasingly important. DFX analysis encourages designers to consider the environmental impact of their products by selecting eco-friendly materials, reducing energy consumption during manufacturing, and designing products that are easier to recycle. This approach helps companies meet regulatory requirements, appeal to environmentally conscious consumers, and contribute to sustainability goals.
How DFX Analysis Works in Product Development
DFX analysis involves a systematic process that incorporates multiple stakeholders in the design process. Here’s an overview of how DFX works:
- Cross-Functional Collaboration: The first step is to involve cross-functional teams, including product designers, engineers, supply chain managers, and manufacturing experts, in the design process. This ensures that all aspects of manufacturability, cost, reliability, and sustainability are considered from the outset.
- Identify Design Requirements: The team defines the key requirements for the product, including functionality, performance, cost targets, and sustainability goals.
- Optimize Design: The team works to optimize the design by focusing on factors such as material selection, production methods, assembly processes, and product testing.
- Iterative Improvement: DFX analysis is an iterative process. As the design progresses, the team continuously evaluates and refines the product to meet the defined requirements and goals.
- Testing and Validation: Before the product is finalized, it undergoes rigorous testing to ensure it meets the performance, reliability, and safety standards. Any issues identified during testing are addressed through further optimization.
Benefits of DFX Analysis Over Traditional Design Approaches
DFX analysis offers numerous advantages over traditional design approaches:
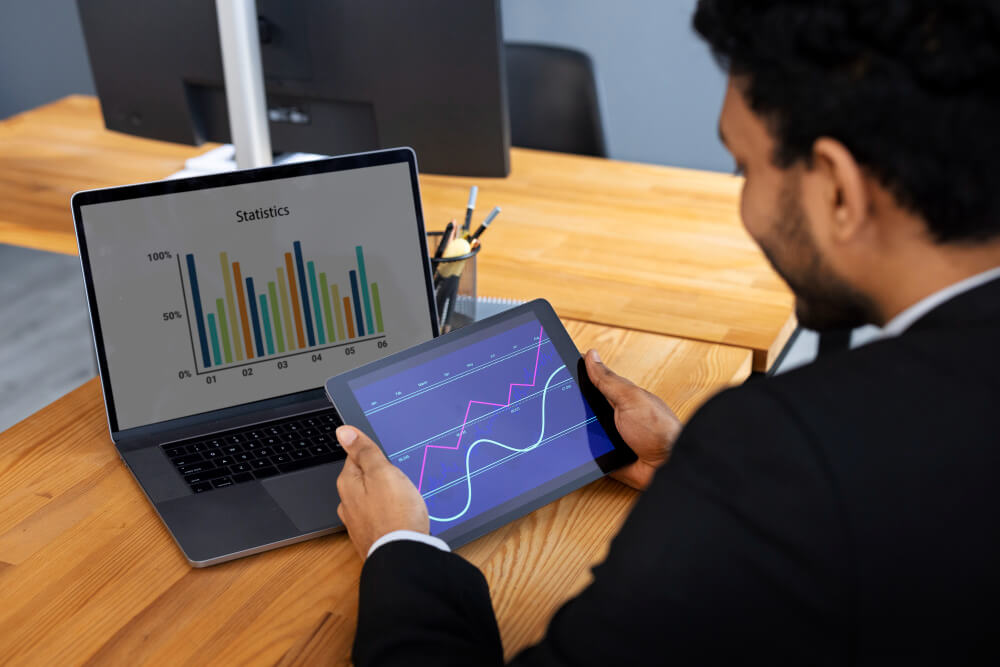
1. Cost Reduction
By addressing cost-related concerns early in the design phase, DFX analysis minimizes the need for costly changes or redesigns later in the process. It helps identify cost-saving opportunities without compromising product quality.
2. Better Collaboration
DFX analysis encourages cross-functional collaboration, ensuring that all teams—design, engineering, manufacturing, and supply chain—are aligned in achieving a common goal. This results in more efficient decision-making and better outcomes.
3. Fewer Production Issues
Since manufacturability and reliability are considered from the beginning, DFX helps identify potential production problems early, reducing the likelihood of defects and delays during manufacturing.
4. Improved Product Performance
By optimizing products for reliability and long-term performance, DFX results in higher-quality products that are more durable and meet customer expectations.
Industries That Benefit from DFX Analysis
1. Automotive Industry
Automotive manufacturers use DFX analysis to design vehicles that are more efficient to produce, reliable, and cost-effective. By considering factors such as material selection, production methods, and assembly, automotive companies can improve vehicle safety, reduce manufacturing costs, and accelerate time to market.
2. Consumer Electronics
In the consumer electronics industry, DFX analysis helps companies design products that are durable, energy-efficient, and easy to assemble. It enables faster development cycles and higher-quality products, such as smartphones, laptops, and wearable devices.
3. Aerospace and Defense
In aerospace and defense, DFX analysis is critical for designing reliable and efficient products that can withstand extreme conditions. It also helps reduce costs while maintaining strict regulatory and safety standards.
4. Medical Devices
For medical device manufacturers, DFX analysis ensures that products meet safety, performance, and regulatory requirements. It also helps reduce manufacturing costs and improve the overall user experience.
How to Implement DFX Analysis in Your Business
To start using DFX analysis in your business, consider these steps:
- Get Buy-In from Leadership: Ensure that leadership understands the value of DFX and supports its integration into the design process.
- Train Your Teams: Provide training on DFX principles to your design, engineering, and manufacturing teams to ensure a common understanding of the approach.
- Adopt DFX Tools: Invest in software and tools that facilitate DFX analysis, including CAD software, simulation tools, and project management platforms.
- Focus on Continuous Improvement: DFX analysis is an iterative process, so continually review your designs and make improvements as needed.
Conclusion
DFX analysis is the key to smarter, more efficient product design. By focusing on manufacturability, cost efficiency, reliability, and sustainability, DFX ensures that products meet customer needs while minimizing waste and reducing costs. Whether in the automotive, aerospace, or consumer electronics industries, businesses that adopt DFX analysis will benefit from enhanced product quality, faster time to market, and improved profitability.