Bringing a new product to market is an exciting but complex journey that requires careful planning, coordination, and execution. The New Product Introduction (NPI) process is a structured approach that helps businesses successfully launch innovative products while minimizing risks and optimizing efficiency. Whether in manufacturing, technology, or consumer goods, mastering the NPI process is essential for ensuring product quality, regulatory compliance, and market readiness.
In this guide, we will cover everything you need to know about the NPI process, including NPI process steps, best practices, common challenges, and how businesses can effectively implement this framework to streamline product launches.
What is the NPI Process?
The NPI process (New Product Introduction) is a structured workflow businesses follow to bring new products from the conceptual stage to mass production and commercialization. It consists of several phases, including idea validation, design, prototyping, testing, production, and market launch. The goal is to ensure that the product meets quality standards, regulatory requirements, and customer expectations before full-scale manufacturing begins.
Unlike the New Product Development (NPD) process, which focuses on product research and design, the NPI process is centered around preparing the product for efficient manufacturing and market entry. Companies that fail to implement a strong NPI framework often experience delays, increased costs, quality issues, and market rejection.
Key Stages of the NPI Process
The NPI process is typically divided into six essential phases that ensure a seamless transition from product concept to commercialization.
1. Concept & Feasibility Analysis
At this initial stage, businesses conduct research to identify market needs, customer demands, and potential challenges. A feasibility study is performed to determine whether the idea is viable, considering factors like:
- Market demand analysis
- Competitor benchmarking
- Technical feasibility and cost assessment
- Risk analysis
If the concept is validated and aligns with business goals, it moves to the next phase.
2. Design & Development
Once the product concept is approved, design and engineering teams create detailed specifications, 3D models, and prototypes. This stage involves:
- Creating CAD (Computer-Aided Design) models
- Developing initial product prototypes
- Assessing design for manufacturability (DFM)
- Performing preliminary testing and analysis
A well-designed product will be easier to manufacture and scale, reducing production errors and inefficiencies.
3. Prototyping & Testing
In this phase, the first functional prototypes are created and tested to ensure they meet performance expectations. This stage includes:
- Functional and durability testing
- User experience feedback collection
- Compliance with industry regulations and safety standards
- Iterative improvements based on test results
By thoroughly testing the product, businesses can identify potential design flaws and make necessary adjustments before full-scale production.
4. Pilot Production & Process Validation
Before launching full-scale production, a limited batch of units is produced to refine the manufacturing process, validate suppliers, and optimize production workflows. This phase focuses on:
- Identifying inefficiencies in the manufacturing process
- Verifying the supply chain and vendor reliability
- Ensuring consistency in product quality
- Adjusting production workflows to improve efficiency
Pilot production is crucial for preventing costly mistakes during mass production.
5. Full-Scale Manufacturing & Quality Control
With a refined and optimized process, full-scale manufacturing begins. At this stage, quality assurance teams implement rigorous testing protocols to maintain consistency and detect defects. Key activities include:
- Automated and manual quality inspections
- Implementation of process control systems
- Finalizing production line adjustments
- Certifications and regulatory approvals
Ensuring a robust quality control process reduces waste, prevents defects, and enhances customer satisfaction.
6. Product Launch & Market Rollout
Once the product is manufactured at scale, it is officially launched to the market. Successful commercialization involves:
- Executing a marketing and sales strategy
- Setting up distribution channels
- Providing customer support and post-launch analysis
- Gathering market feedback for future improvements
At this stage, businesses focus on product positioning, branding, and customer engagement to ensure a strong market entry.
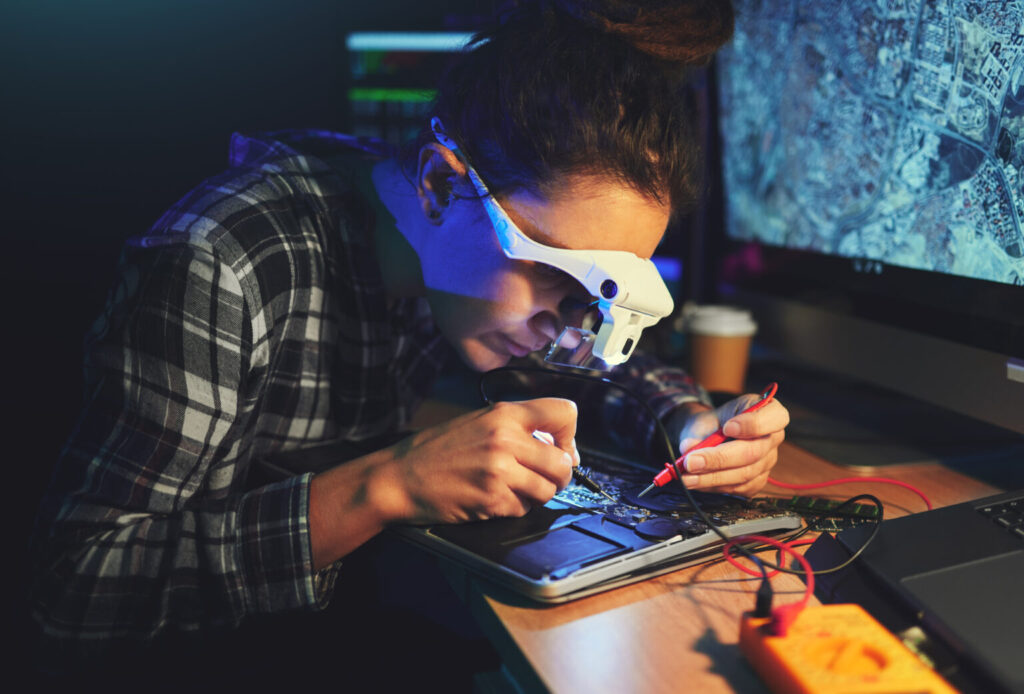
Best Practices for a Successful NPI Process
To optimize the NPI process, companies should adopt industry best practices, including:
- Cross-Functional Collaboration: Encouraging strong communication between R&D, engineering, supply chain, and marketing teams to prevent silos.
- Robust Testing Procedures: Implementing early-stage testing and validation to minimize design flaws and quality issues.
- Supplier & Vendor Engagement: Working closely with manufacturers and material suppliers to prevent bottlenecks in the supply chain.
- Agile & Lean Manufacturing Principles: Adopting flexible and iterative processes to adapt to market changes and customer feedback.
- Regulatory Compliance & Certifications: Ensuring all products meet industry safety, environmental, and regulatory standards before launch.
Common Challenges in the NPI Process
Despite having a structured approach, companies often face challenges during new product introduction:
- Time-to-Market Pressure: Balancing speed and quality while ensuring timely product launch.
- Supply Chain Disruptions: Managing material shortages, production delays, and vendor reliability.
- Budget Constraints: Controlling manufacturing and operational costs without compromising quality.
- Design Iterations & Revisions: Handling continuous product improvements and feature changes that may lead to delays.
Proactively addressing these challenges with efficient planning, risk mitigation strategies, and agile management ensures a smoother NPI process.
Conclusion
The NPI process plays a pivotal role in the successful introduction of new products. By following a structured framework that includes concept validation, prototyping, testing, and quality control, businesses can reduce risks, enhance efficiency, and achieve faster market adoption.
Companies that prioritize strategic planning, cross-team collaboration, and continuous improvement are more likely to launch high-quality products that meet customer needs and drive business growth.
Whether you’re in manufacturing, technology, or consumer goods, implementing a robust NPI framework will help your company stay competitive and deliver successful product launches.