In the competitive world of product design, success hinges on creating products that are efficient, reliable, and cost-effective. Design for Excellence (DFX) analysis is a strategic framework that helps businesses achieve these goals by optimizing various aspects of the design and development process. By incorporating DFX principles early in the design phase, companies can reduce costs, improve product quality, and enhance customer satisfaction. This blog explores the fundamentals of DFX analysis and how it drives maximum efficiency in product design.
What Is DFX Analysis?
DFX, or Design for Excellence, is a holistic approach to product design that focuses on optimizing specific elements such as manufacturability, reliability, cost, and sustainability. Unlike traditional design methods, DFX incorporates cross-functional collaboration between engineering, manufacturing, and quality assurance teams to identify and resolve potential challenges during the design phase. This proactive approach ensures that products are designed for optimal performance throughout their lifecycle.
The Key Elements of DFX
- Design for Manufacturability (DFM): DFM ensures that the product can be manufactured efficiently at scale. It focuses on simplifying the design, reducing production steps, and minimizing the use of complex or expensive components.
- Design for Reliability (DFR): DFR emphasizes creating products that perform consistently under various conditions. This involves rigorous testing and material selection to ensure durability and dependability.
- Design for Cost (DFC): DFC aims to minimize production costs without compromising quality. By optimizing material usage and manufacturing processes, companies can achieve cost savings while maintaining high standards.
- Design for Sustainability (DFS): DFS focuses on creating eco-friendly products by reducing waste, using sustainable materials, and designing for recyclability.
- Design for Assembly (DFA):
DFA ensures that the product can be assembled efficiently, reducing labor costs and assembly time.
The Role of DFX in Product Development
DFX plays a crucial role in streamlining product development. By identifying potential challenges early, it reduces the need for costly revisions during later stages. For example, during the prototyping phase, DFM can highlight manufacturing bottlenecks, enabling teams to adjust designs before full-scale production begins. This not only saves time but also minimizes resource wastage.
Benefits of DFX Analysis
- Improved Product Quality: DFX principles ensure that products are designed to meet high-quality standards. This reduces defects and enhances customer satisfaction.
- Cost Savings: By focusing on efficiency and optimization, DFX minimizes material and production costs. This approach also reduces the likelihood of expensive recalls or redesigns.
- Faster Time-to-Market: Addressing potential issues during the design phase accelerates the development timeline, enabling businesses to launch products more quickly.
- Sustainability: DFX promotes sustainable practices, reducing the environmental impact of production and end-of-life disposal.
- Enhanced Collaboration: DFX encourages cross-functional teamwork, fostering better communication and alignment between design, manufacturing, and quality assurance teams.
Practical Applications of DFX Analysis
- Consumer Electronics: In industries like consumer electronics, DFX ensures compact, efficient designs that are easy to manufacture. For instance, smartphones incorporate DFM to optimize the placement of components on circuit boards, reducing production complexity.
- Automotive Industry: Automotive manufacturers use DFR to design durable components that can withstand harsh conditions, such as extreme temperatures and heavy vibrations.
- Medical Devices: In healthcare, DFX ensures that devices meet stringent quality and regulatory standards while remaining cost-effective.
- Simplifying Manufacturing Processes: By reducing the number of parts and assembly steps, DFX minimizes production errors and speeds up manufacturing.
- Reducing Material Wastage: Optimizing material usage during the design phase ensures cost savings and supports sustainable practices.
Challenges in Implementing DFX
Despite its benefits, implementing DFX analysis can be challenging.
- Initial Investment: DFX requires advanced tools and skilled professionals, which can lead to higher upfront costs.
- Cultural Resistance: Shifting from traditional design methods to DFX may face resistance from teams unfamiliar with this approach.
- Balancing Trade-Offs: Optimizing one aspect (e.g., cost) may affect another (e.g., reliability). Effective implementation requires careful balancing of competing priorities.
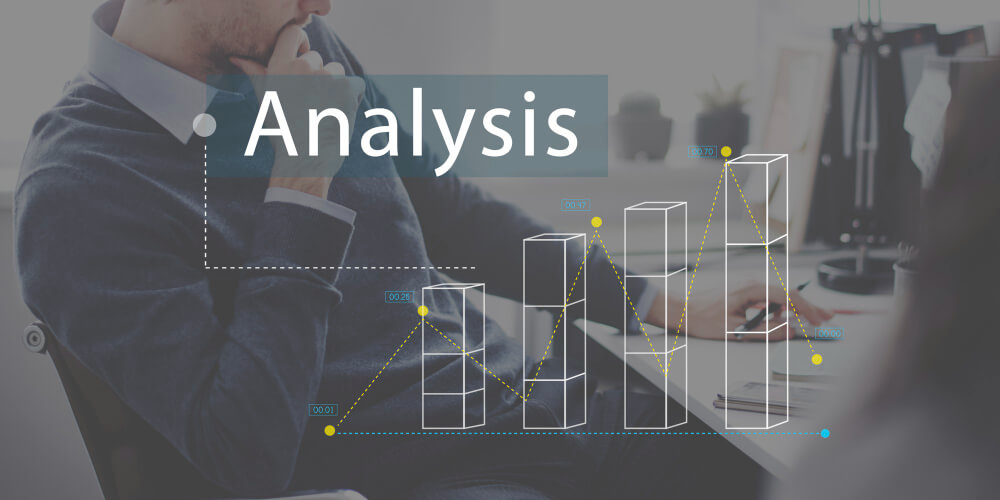
How to Implement DFX Successfully
- Invest in Training and Tools: Equip your teams with the knowledge and resources needed to apply DFX principles effectively.
- Foster Collaboration: Encourage cross-functional communication to ensure all stakeholders are aligned on design goals.
- Leverage Technology: Use advanced design software and simulation tools to identify and resolve issues early.
- Iterative Testing: Conduct regular testing throughout the design process to validate assumptions and refine designs.
Real-World Success Stories
- Boeing: Boeing’s use of DFX in aircraft design has streamlined production and reduced manufacturing costs while ensuring safety and reliability.
- Apple: Apple employs DFX to create sleek, efficient products like the MacBook, balancing aesthetics, performance, and manufacturability.
- Tesla: Tesla’s focus on DFM and DFA has optimized the production of electric vehicles, enabling the company to scale operations rapidly.
The Future of DFX Analysis
As industries evolve, DFX will continue to play a critical role in product development. Emerging technologies like artificial intelligence (AI) and machine learning are expected to enhance DFX by providing deeper insights into design optimization. Additionally, the growing emphasis on sustainability will drive innovation in eco-friendly materials and processes, further expanding the scope of DFX.
Conclusion
DFX analysis is a transformative approach to product design that prioritizes efficiency, reliability, and cost-effectiveness. By addressing potential challenges during the design phase, it ensures superior product quality, faster time-to-market, and long-term sustainability. Whether you’re in consumer electronics, automotive, or healthcare, incorporating DFX principles into your design process is a proven way to achieve maximum efficiency and stay ahead in a competitive market.
Businesses that embrace DFX are not just designing products—they’re designing excellence.