COATING CONFORMAL addresses several concerns which are environmental and operational factors affecting modern electronics. In the manner that it envelops the electrical parts protects them from the effects of moisture, dust, other chemicals, and varying temperatures,. But how does this coating make a difference and provide the highest performance than any other coating type to have long-lasting?
Want to know how Coating Conformal protects against environmental stress?
Electronics are vulnerable to different types of conditions for instance high humidity areas, dust or corrosive environments. Conformal coatings can also be considered as an insulating layer which shields sensitive components from contaminants. This guarantees that devices work to their optimum best especially when operating in complex environments and minimizes the incidences of failures.
Why Is Moisture Resistance Such an Essential Attribute for Electronics Durability?
In the circuits, moisture normally causes the effect of short-circuiting, corrosion or even total failure. Information concerning conformal coatings can be supplemented by the understanding that they are excellent barring moisture because they form a barrier against humidity. Marine, automotive, and aircraft industries some among them rely on this feature to ensure they maintain the reliability of their equipment.
In What Way Does Hydrophobicity Help Guard Circuits
Hydrophobic conformal coatings do not allow water molecule closeness hence non-conductivity and prevent the formation of electrical shorts or corrosion hence enhanced performance under wet conditions.
Companies that gain from moisture resistance
Innovations ranging from outdoor sensors to industrial machinery cannot be produced without using this protection to increase the sturdiness of devices.
How Does Corrosion Resistance Work to Change the Game?
Metals used in electronics corrode easily when exposed to oxygen, salt or any industrial chemical. Such reactions are avoided because conformal coatings help seal off metal surfaces. Not only does this help to increase the longevity of the devices, but probably their efficiency does not decrease over time.
Does Thermal Stability play a role in increasing Operational efficiency?
At elevated temperature conditions, the components of electronics are susceptible to degrading due to heat stroke. Heat-resistant conformal coatings are those that possess thermal stability and can withstand the challenging thermal regime for an electronic gadget without degrading the device. This makes them useful in manufacturing organizations, for example, in aerospace companies.
How You May Benefit from Electrical Insulation?
These include: shorts between electrical contacts on devices which cause them to fail or become dangerous. Conformal coatings are highly effective in offering the electrical insulation necessary to avoid circuit connections. This reduces risks and enhances the efficiency of such devices, especially in high-density electronics assembly.
What makes flexibility important for the electronics industry?
Today electronics have undergone mechanical stress, vibrations and motion. Semiflexible conformal coatings befit these conditions in a manner that will not form cracks or depopulate, and the protection continues. The flexibility reaps big benefits in cars, aircraft, and wearable applications.
In What Ways Chemical Resistance Properties Protect Industrial Devices?
Commonly in industries, some solutions attack electronics and cause the deterioration of their parts. Conformal coatings shield against chemicals in preserving the performance and reliability of electronic devices. This feature is particularly appreciated in factories, laboratories and chemical plants.
Do Outside Paints Require UV-Resistant Coatings?
UV affects the electro-optical properties of many materials used in the fabrication of these devices and therefore affects the performance of the outdoor displays. Organic UV conformal coating covers the devices to guard them against wearing by the sun’s light. Such applications as solar, telecommunications, and outdoor sensors are among the many that can greatly benefit from this feature.
How does Precision Application enhance the performance of the Coating?
Conformal coatings are also used in applications where the correct application of the conformal coating is the major determinant of the effectiveness of the conformal coating. Minerals coated today come with unique technologies such as newly developed selective coating machines that provide an even coat without the formation of overspray or leftover product. Such precision reduces the cost expenditure as much as it protects effectively hence enhancing the efficacy of the process.
What’s Next in the Evolution of Coating Conformal?
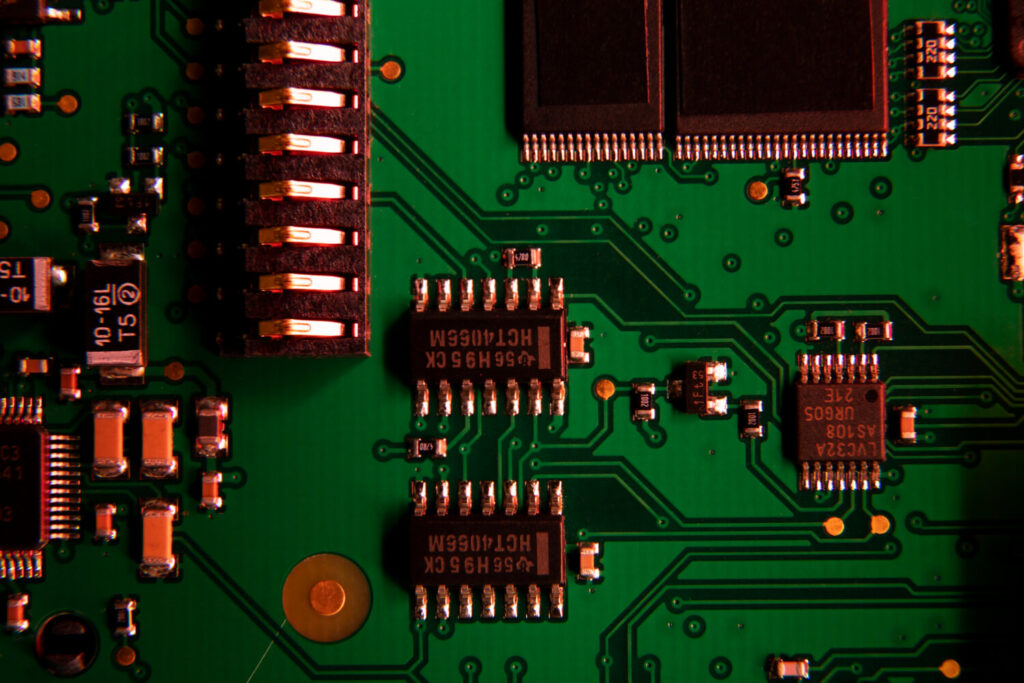
Relatively, innovation propels the future of conformal coatings. There are already Nano-coatings, bio-based solutions, and self-healing materials that are going to be developed to attend to the needs of advanced electronics. The progress and innovations here offer protection, environmental sensitivity and flexibility that are incomparable and mark new highs in endurance.
Final Thoughts
Coating Conformal is an essential resource for improving the life cycle of modern electronics. Ageing is overcome, corrosion is avoided, it exhibits thermal and mechanical shock, and these uses cut across industries and markets. Modern technologies are constantly developing along with conformal coatings and that’s why they are still relevant to electronic protection. Thus, the adoption of sucha solution will help organizations improve the performance of their products, lower the costs of maintenance of such devices and increase the confidence of customers due to the reliability and sturdiness of particular products.