Engineering isn’t just about solving problems—it’s about solving them smartly, efficiently, and with the future in mind. That’s where DFX (Design for X) enters the chat. DFX is not a new buzzword; it’s a framework that ensures a design is optimized for specific outcomes like manufacturability, reliability, cost, and sustainability. But here’s the kicker: DFX has evolved massively over the years, keeping pace with modern tech and methodologies.
The Origins of DFX
Back in the day—think mid to late 20th century—manufacturing was the kingpin. The first whispers of DFX were mostly about Design for Manufacturability (DFM). Engineers realized that designing something cool meant nothing if it was a nightmare to build. This initial focus on manufacturability laid the foundation for what would become an entire ecosystem of design-focused strategies.
The Core Philosophy Behind DFX
At its core, DFX is about “designing with intent.” The “X” can stand for manufacturability, assembly, reliability, cost, sustainability—you name it. The goal? Design once and design smart. It’s like baking a cake knowing it has to survive a road trip—you’re not just focused on taste, but also on durability and portability.
The Major Types of DFX
Design for Manufacturability (DFM)
DFM is the OG of DFX. It’s all about making sure a product can be made with the least hassle, cost, and waste. Want to use exotic materials that require special tools? Better think twice.
Design for Assembly (DFA)
This one ensures that your product isn’t a puzzle with missing pieces. DFA focuses on reducing parts, simplifying joints, and ensuring efficient assembly—especially important in mass production.
Design for Reliability (DFR)
No one likes a product that gives up after a few uses. DFR helps ensure that your design can handle stress, time, and user abuse without throwing in the towel.
Design for Testability (DFT)
If it breaks, how do we find out what went wrong? DFT bakes in the ability to test and diagnose systems easily.
Design for Sustainability (DFS)
This one’s for Mother Earth. DFS ensures that a product’s environmental impact is minimized across its entire lifecycle—from raw materials to disposal.
The Evolution Over the Decades
1980s to 2000s: Traditional DFX Methods
In this era, DFX was mostly manual and paper-based. Engineers relied on experience and checklists. It worked, but it was slow and often reactive.
The Rise of Simulation Tools
Enter CAD, CAE, and simulation tools. Suddenly, engineers could test ideas virtually before building them. DFX became faster, more accurate, and predictive.
Integration with CAD/CAE
Modern CAD systems aren’t just drawing tools anymore—they come with built-in DFX analysis. Engineers can now run real-time checks for manufacturability, stress, tolerance, and more, right from their desktop.
Modern Engineering and DFX
Cross-Functional Teams & Agile Engineering
Today, design isn’t done in silos. Teams from engineering, manufacturing, marketing, and even customer service collaborate early in the process, bringing multiple perspectives into DFX decisions.
AI and Data-Driven DFX
Machine learning algorithms now help predict failure points, optimize part geometry, and even suggest better materials—all in real-time.
Cloud Collaboration and Real-Time Feedback
Design teams spread across the globe can work together seamlessly thanks to cloud platforms. Real-time feedback = faster iterations and smarter decisions.
Industry-Specific Applications
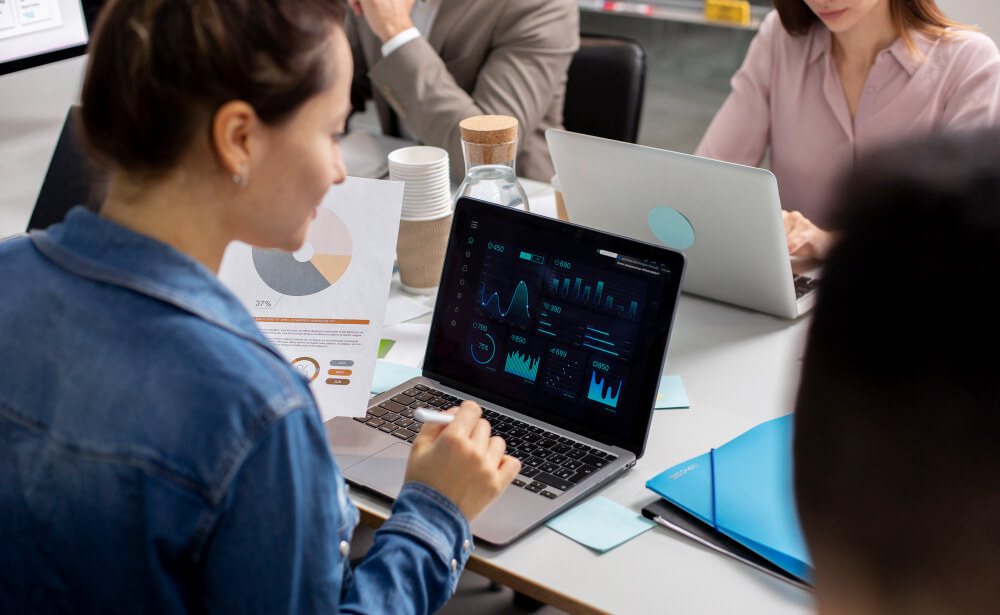
Aerospace and Defense
DFX in aerospace focuses heavily on safety, reliability, and weight. Even a tiny design flaw can have catastrophic results.
Consumer Electronics
In gadgets, the focus is on miniaturization, assembly, and cooling. DFX helps manage thermal issues and make products easier to assemble on a large scale.
Automotive Sector
DFX here is about cost, reliability, and sustainability. Think electric vehicles, where battery safety and environmental impact are huge concerns.
Medical Devices
With strict regulations, DFX in medical device design emphasizes testability, reliability, and ease of sterilization.
The Benefits of Evolving DFX Practices
- Cost Savings: Smart design = less rework.
- Time Efficiency: Solve problems before they happen.
- Better Product Performance: Optimize across multiple parameters from the get-go.
Common Challenges in Implementing DFX
- Resistance to Change: Old habits die hard.
- Complexity in Integration: Plugging DFX into existing workflows isn’t always seamless.
- Lack of Standardization: Every company has its own spin on DFX.
The Role of Software and Automation in DFX
Tools like SolidWorks, Siemens NX, and Ansys are revolutionizing DFX. These platforms offer integrated simulation, material analysis, and manufacturability checks.
The Human Element in DFX
Let’s not forget the people behind the process. Even the best tools need skilled engineers who understand both the tech and the philosophy of DFX. Training and collaboration are crucial.
Sustainability and DFX
Sustainable design is no longer optional. Companies are embracing eco-design, using recycled materials, and designing products for disassembly and reuse.
The Future of DFX
The next frontier? Predictive analysis, AI, digital twins, and virtual prototyping. Imagine testing thousands of design iterations in a digital universe before building a single prototype. That’s not sci-fi—it’s happening.
Conclusion
DFX isn’t just an engineering checkbox—it’s a mindset. From humble beginnings in manufacturability to a comprehensive strategy covering everything from sustainability to testability, DFX has grown alongside technology. In today’s high-speed, high-stakes engineering world, evolving your DFX approach isn’t just smart—it’s essential.